Safran breakthrough channels communication to a new level
Communications technology provides answers for improving the safety, efficiency and cost of line and base maintenance operations. Chuck Grieve has been finding out more.
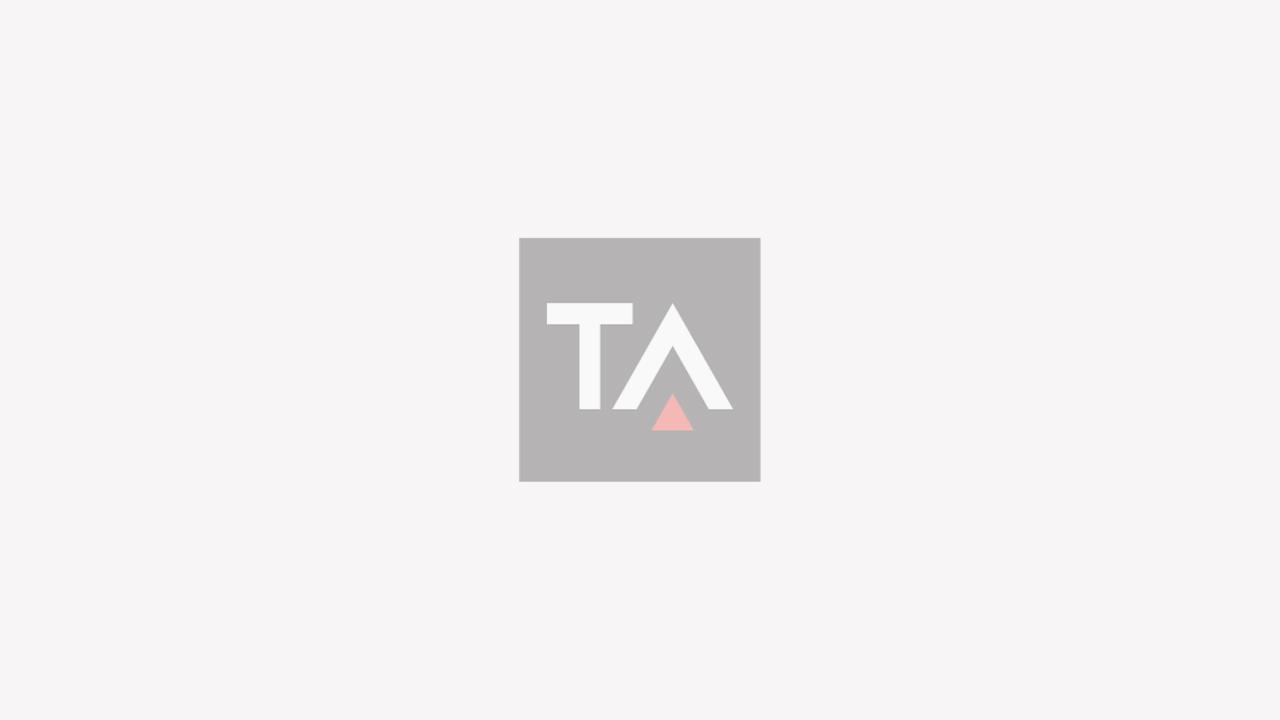
A new support service and tool for borescope inspections (BSI), just launched by Safran Aircraft Engines, is being heralded as a breakthrough for the MRO industry.
Called B.SIde, it uses a bundle of communication channels, including live two-way video, to connect technicians in the field with an engine expert.
The service is designed to support remote critical inspection in real time, around the world. It was demonstrated at MRO Middle East, ahead of its commercial launch in April.
B.SIde emerged from innovation workshops that brought together end-users, Safran experts and product developers to discuss how to simplify BSI. It has been piloted with customers, including Luxembourg-based Luxair, and Safran’s own on-wing support teams have been using it since autumn 2017.
Marcellette Cloche, business developer, services and MRO division, said workshop participants underlined the need to use “all channels, including voice and video, for effective communication. It’s important to be able to see the person you’re talking to.”
She told delegates to the Airline Engineering & Maintenance conference in Dubai that B.SIde was designed as a “relatively inexpensive” way to enhance collaboration and improve BSI productivity. In operation, it also promises to shorten the learning curve for engine technicians and improve their skillsets.
The tool comprises a video converter and ergonomic web platform and is compatible with all types of borescope and hand-held communication devices, including smart phones and tablets. Users can collaborate through voice, photos, video, document sharing and live conferencing with any number of participants. For precision and clarification, they can mark up the photos and videos they share.
B.SIde also gives users a checklist and report generation function that automatically organises photos, comments, sanctions and electronic signatures. Using the B.SIde cloud centralises all relevant documents on the engine’s health and allows them to be shared.
“Technicians can encounter new situations, whether they’re doing line or base maintenance, that prevent them from signing off the engine inspection report,” said Cloche. “Particularly in remote locations, this could cause delay and disruption and add cost.”
Using Safran’s new tool, technicians can ask for support, discuss the case with an expert, share images and videos, and together resolve the situation.
“B.SIde then generates the appropriate report and the aircraft can take off.”
Safran also sees good potential for B.SIde for sharing and issuing reports internally, for scheduled assistance and on-the-job training, and for aircraft-on-ground (AOG) help. And, while it was designed for borescope inspections, technicians could also use the tool in the same way for outside-of-engine or piece-part inspections.
The aircraft technician’s need for a simplified process – in this case for documentation – is also the rationale behind a voice-activated system from Honeywell to be adopted by Abu Dhabi’s TS&S Aerospace.
The two companies used MRO Middle East as the stage for signing an agreement making the Abu Dhabi-based company Honeywell’s first Middle East customer for its maintenance and inspection (M&I) voice system.
TS&S Aerospace said it is a significant step toward realising the company’s ambition of digitising its processes with data-generated solutions, known as smart connected assembly.
The Honeywell system uses advanced voice and sound-recognition algorithms to create a ‘hands-free, eyes-free’ environment in which technicians can log their observations and diagnoses in real time by speaking into a simple headset with a remote network connection.
Honeywell says its system can significantly reduce paper-based documentation and cut the amount of manual data entry. Users typically see a 35% improvement in productivity and 25% reduction in operational errors, the company says.
TS&S plans to automate processes in its materials requirement planning (MRP) system using the new voice capability.
Stay up to date
Subscribe to the free Times Aerospace newsletter and receive the latest content every week. We'll never share your email address.