Feedback's crucial role in designing better aircraft
How much do engineers in the field and in MRO shops contribute to shaping current and future programmes? Plenty, say those who know. Chuck Grieve reports.
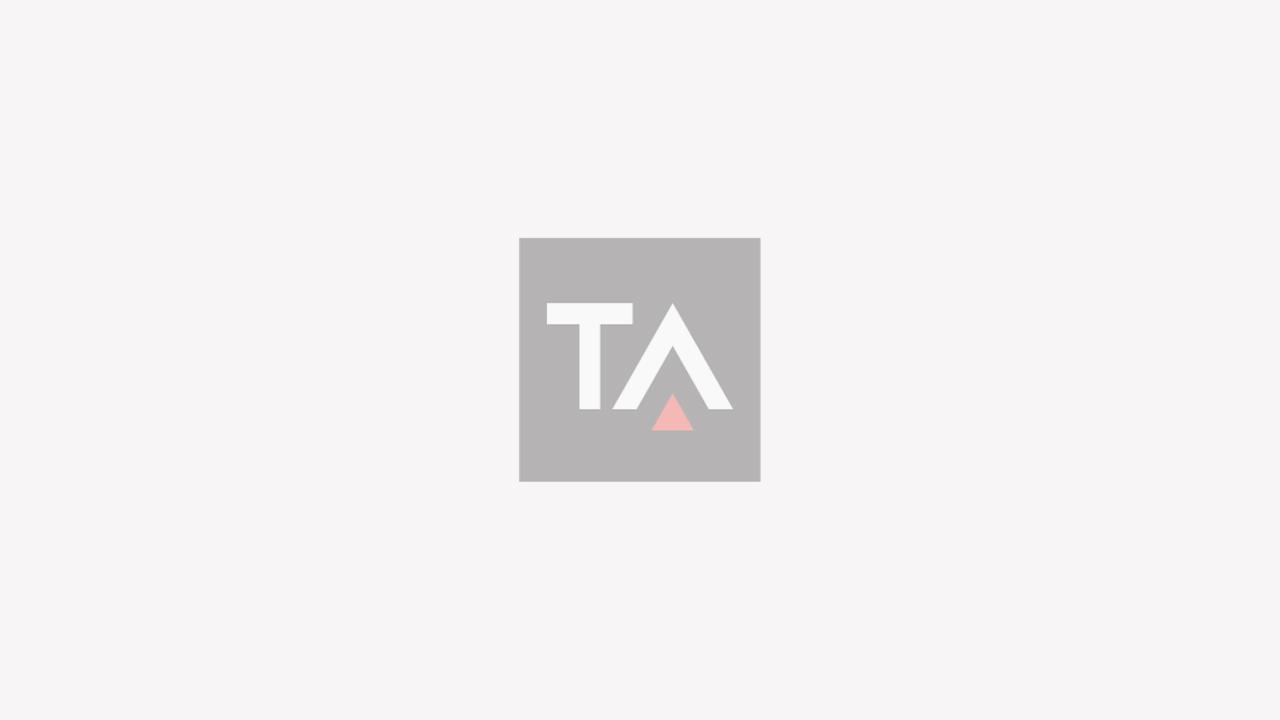
Climatic conditions in the Middle East are notoriously hard on machines. The summer heat, humidity, salty and grit-filled air can – and do – damage aircraft and aero engines when they are operating and when they are static.
In few other environments is the feedback loop between MRO and line engineers and original equipment manufacturers (OEMs) as important in maintaining airworthiness.
When Boeing’s David Longridge, vice-president commercial services, said the Seattle airframer would be able to design “even better aircraft” by expanding its aftermarket presence, he was overlooking the ‘virtuous circle’ that already exists between manufacturers, operators and those who regularly see what happens to aircraft after they leave the factory.
Feedback is a “constant in the industry”, whether it comes from an MRO or OEM facility, said Nick Weber, maintenance director of ExecuJet Middle East.
Anne Lilywhite, director of engineering for Honeywell Aerospace, said feedback plays “a critical role in the R&D process. It encourages new ideas and helps us deliver on our promise of continuous innovation.”
And Dr Oliver Reichel-Busch, head of corporate idea management at Lufthansa Technik (LHT) added: “Engineers want to make things better. It’s in our DNA.”
Feedback from engineers has led to innovative new programmes and systems. It also prompts improvements in current programmes, notably through new service bulletins and airworthiness directives (ADs).
ExecuJet has instigated several of each since 2006, when the company, part of the Luxaviation Group, established MRO facilities for a range of business jets in Dubai. They were based on issues found and reported to the relevant OEMs, said Weber.
“We regularly provide information back to OEMs,” he said. Any work outside the approved maintenance data needs approval and guidance; once raised, an issue will receive OEM attention until it’s resolved.
The Middle East climate is known to cause corrosion across all aircraft types. Windshields appear to be particularly vulnerable, said Weber, suffering higher failure rates in the region than elsewhere due to grit in the air.
Surface treatment and exterior refurbishment suppliers are also looking at improved ways of protecting surfaces in general, he added.
More generic fleet issues are also detected. “We found an issue with the flaps of an aircraft operating in the region,” said Weber. “The flap’s bushings/bearings were migrating. We reported this back to OEM. This led to an advisory.
“When the OEM started looking into it, it uncovered several more aircraft with similar problems. Now there’s a global campaign to rework the area.”
For Honeywell Aerospace, feedback from engineers is hugely important in product development. “We’re constantly challenging our engineers to come up with new ideas,” said Lilywhite.
You can’t rush engineering feedback, especially with technologies as advanced as Honeywell’s SmartPath ground-based augmentation system and the connected weather radar. “Time can be the difference between sharing a technology that’s ready for use after testing and sharing something that won’t meet the customer’s goals,” she said.
It’s important enough for Honeywell to have formalised the process in Europe with an innovation council and innovation events. Company engineers can present ideas to the council to win funding for further development. The innovation events update leadership teams on new ideas.
“This kind of open forum ensures recognition of ideas and allows research to be shared among relevant teams,” said Lilywhite. “More often than not, we incorporate engineer feedback and ideas into Honeywell technologies.”
One example is the traffic collision avoidance system (TCAS). “The engineering team turned it into a competitive product by adding coupled autopilot, a feature that predicts dangerous collisions in the vicinity and automatically steers the aircraft away from them.
“The automated concept ensures a quick change in route, without harming passengers with an aggressive dive or climb.”
Processes also benefit from shop-floor feedback. LHT realised it saves around €40 million ($47 million) a year by implementing creative ideas from its technicians, so in 2016 it formalised a programme of encouraging creative thinking and called it ‘my ideas’.
“It’s important to us that all those involved in the company, from the idea generators to the experts and company executives to top management, devote the necessary attention to the topic,” said Reichel-Busch. “Only then can the enormous potential of employee ideas be made permanently available to the company.”
The new idea management concept uses streamlined processes and modern IT to make it easy to submit an idea, verify it and decide on its implementation. LHT expects it to be rolled out internationally this year.
Results from ‘my ideas’ spread quickly, said Reichel-Busch. When a laborious process for recording data from damage analyses frustrated a team of LHT mechanics in Hamburg, they developed an app that combined several steps into one. The new app takes one to three minutes, instead of up to 10 minutes per process with the old approach, to link a photo taken on a tablet PC to a barcode from the order sheet and add them to the report in the system.
More than 50 departments are already using this in-house development. With thousands of recordings like these every year, the savings potential is enormous.
Boeing, in addition to advancing its understanding of what happens to aircraft when they leave the factory, sees logic in wanting to increase its aftermarket presence. Its aircraft account for 50-60% of the global fleet, said Longridge, while its share of the aftermarket is estimated at 7%.
There is evidence that airlines are not entirely happy about the big civil aviation prime contractors increasing their direct involvement in MRO. “We don’t support it,” Heiko Holm, chief technology officer at Wizz Air, was quoted as saying. “We’d rather maintain competition.”
Although global consultancy ICF International foresees “a more consolidated market” with OEMs taking a larger share of MRO, Airbus argues that Boeing and itself are actually “medium-sized players” in MRO.
Laurent Martinez, senior vice-president for services at Airbus, observes that the aftermarket is more fragmented and competitive than aircraft manufacturing.
And far from pushing smaller players out of the MRO market, Boeing expects to be teaming up with them.
“We need help around the world for our airline customers to actually implement the work we’re planning, so we use MROs globally to achieve this and will continue to do so,” Longridge told an audience at MRO Asia-Pacific in November. “I would advocate that there is plenty of room [in the wider aftermarket] for everyone.”
Stay up to date
Subscribe to the free Times Aerospace newsletter and receive the latest content every week. We'll never share your email address.