Awakening the digital sleepers
Product lifecycle management (PLM) is more important now than ever as complexity in products and processes skyrockets and digitalisation becomes the norm. Chuck Grieve looks at some approaches to this challenge.
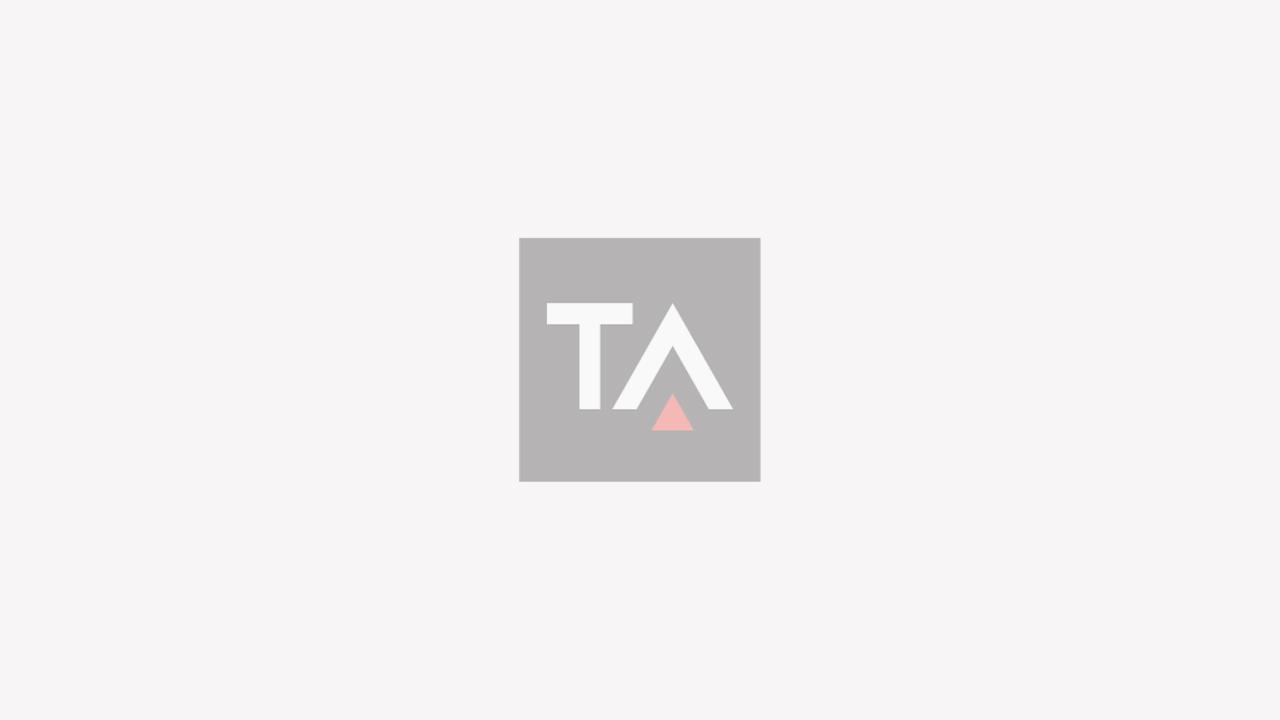
Complexity is the hallmark of the modern era, and few places more so than aviation. Not only are aircraft and their systems increasingly complex, the myriad laws and regulations governing every aspect of their lifecycle demand pin-sharp attention to detail for compliance.
Enter product lifecycle management (PLM), a philosophy and the systems to support it.
PLM is the digital gateway for people to access critical information and work with others in different disciplines throughout the product lifecycle, from design and manufacturing to service and repair.
With its origins in automotive engineering and military aviation, PLM has become a key element of modern manufacturing and subsequent aftermarket processes. Its value lies in managing complexity with effective information and communication technology (ICT).
Graham McCall, vice-president operations UK for software provider, Aras, has observed that an emphasis on engineering leaves some PLM systems weak in other processes critical to developing, manufacturing and supporting profitable products. What’s needed, he said, is resilience.
Writing for ADS Advance, McCall said the four key functions of a resilient platform are to provide contextual information, coordination, collaboration and management throughout a product’s lifecycle. “A resilient platform... is fundamental to breaking down barriers and building trust in data, so teams can work together efficiently and effectively.”
Boeing’s Ted Colbert, newly appointed to lead Boeing Global Services (BGS), told Arabian Aerospace at the recent Dubai Airshow that he believes the biggest ‘sleeper’ area of growth could be digitisation – leveraging new opportunities that take advantage of data to support decision-making: “To inform the operator, inform the mechanic, inform the planner.”
Lifecycle management is, of necessity, a partnership between OEMs and their customers. Boeing identifies its various digital monitoring and management tools as Boeing AnalytX. A spokesman said AnalytX is neither a single software application nor “just a platform”; rather it represents a collection of services and solutions designed to help operators improve situational awareness, increase performance and optimise processes.
In the MRO space, Boeing recently deployed its Boeing optimized maintenance program with Emirates across the Dubai carrier’s 777 fleet. This programme is designed to bring together Boeing airline operations consulting expertise and data analytics software to evaluate an airline’s fleet maintenance programmes.
The Boeing spokesman said Emirates maintenance and engineering executives were “pleased” with the programme, which was implemented last January. He added that Emirates had noted benefits, including additional revenue operation days for the fleet, an increase in hangar availability, a reduction in resource and material requirements, and overall financial savings.
PLM can be applied at different stages. Lufthansa Technik (LHT) embraces the concept in its VIP aircraft services division which, it says, is designed to support owners “in every facet of the lifecycle of an aircraft” from selection through green-aircraft completion to aftermarket.
Last year, LHT took a decisive step in digital transformation by adopting the Windchill PLM platform. LHT planned to use Windchill as an “engineering backbone”, enabling R&D and manufacturing to work concurrently and improve collaboration, both internally and among its many suppliers.
Dr Severin S Todt, LHT’s senior director IT completion and design solutions, said: “The magnitude of our organisation, combined with the complexity of the processes and projects we drive, made the dedicated step to across-the-board digital transformation imperative.”
As a systems OEM, Liebherr-Aerospace is on almost every large civil aviation programme, and backs up its OEM role with a ‘cradle-to-grave’ approach covering MRO, engineering support, documentation, new spares and even used serviceable material (USM).
The company recently developed a centralised procurement structure for its USM, managed from its Dubai Service Centre. Damon Seksaoui, aerospace division general manager for Liebherr Middle East, said: “This involves analysing aircraft teardown forecasts and selecting Liebherr parts to feed ‘USM by Liebherr’ certified parts towards customers supporting this line of business.”
Joel Cadaux, the company’s director business and services – customer services, said PLM “is in the core values of the Liebherr Group. We are committed to delivering full product lifecycle support, from entry-into-service to end-of-life.”
Stay up to date
Subscribe to the free Times Aerospace newsletter and receive the latest content every week. We'll never share your email address.